1 總 則
1.0.1 為規范油氣田含硫化氫天然氣地面設施所用的抗硫化物應力開裂和(或)抗應力腐蝕開裂的金屬材料及其制造工藝的要求,特制定本規范。
1.0.2 本規范適用于按常規的彈性準則設計和制造設備所用與含硫化氫介質接觸的天然氣地面設施的金屬材料,包括井場、站場、處理廠的工藝設備、工藝管線及采、集氣管線等。本規范不包括硫化氫引起的電化學失重腐蝕和其他類型的開裂。
1.0.3 天然氣地面設施用抗硫化物應力開裂和(或)抗應力腐蝕開裂金屬材料除應符合本規范外, 尚應符合國家現行的有關標準的規定。
2 術語和縮略語
2.1 術語
2.1.1 硫化物應力開裂 sulfide stress cracking
在有水和硫化氫存在的情況下,與腐蝕、殘留的和(或)施加的拉應力相關的一種金屬開裂。
2.1.2 應力腐蝕開裂 stress corrosion cracking
在有水和硫化氫存在的情況下,與局部腐蝕的陽極過程、殘留的和(或)施加的拉應力相關的一種金屬開裂。
注:氯化物和(或)氧化劑和高溫能增加金屬產生應力腐蝕開裂的敏感性。
2.1.3 氫致開裂 hydrogen-induced cracking
為氫原子擴散進鋼鐵中并在陷阱處結合成氫分子(氫氣)時所引起的在碳鋼和低合金鋼中的平面裂紋。
2.1.4 酸性環境 sour service
含有硫化氫并能夠引起金屬材料發生硫化物應力開裂、應力腐蝕開裂、氫致開裂等開裂形式的 油氣田環境。
2.2 縮略語
2.2.1 AYS——實際屈服強度
2.2.2 HBW——布氏硬度
2.2.3 HIC——氫致開裂
2.2.4 HRB——B 標尺洛氏硬度
2.2.5 HRC——C 標尺洛氏硬度
2.2.6 HV——維氏硬度
2.2.7 SSC——硫化物應力開裂
2.2.8 SCC——應力腐蝕開裂
2.2.9 SMYS——規定最小屈服強度
2.2.10 SSRT——慢應變速率試驗
3 一般規定
3.0.1 用于酸性環境的管道及設備的設計、制造和施工應選擇抗 SSC 和(或)抗 SCC 的碳鋼、低合金鋼和耐蝕合金,采用抗 SSC 和(或)抗 SCC 的焊接工藝和焊材,并應符合現行國家標準《石油天然氣工業 油氣開采中用于含硫化氫環境的材料 第 1 部分:選擇抗裂紋材料的一般原則》GB/T
20972.1、《石油天然氣工業 油氣開采中用于含硫化氫環境的材料 第 2 部分:抗開裂碳鋼、低合金鋼和鑄鐵》GB/T 20972.2 和《石油天然氣工業 油氣開采中用于含硫化氫環境的材料 第 3 部分:抗開裂耐蝕合金和其他合金》GB/T 20972.3 的規定。
3.0.2 碳鋼或低合金鋼發生SSC的酸性環境的嚴重程度應按下列規定進行劃分:
1 碳鋼或低合金鋼發生SSC的酸性環境的嚴重程度應采用圖3.0.2根據硫化氫分壓(
PH S )和溶液的原位pH值進行評價。PH S <0.0003MPa的環境為0區, PH S ≥0.0003MPa的環境分
2 2 2
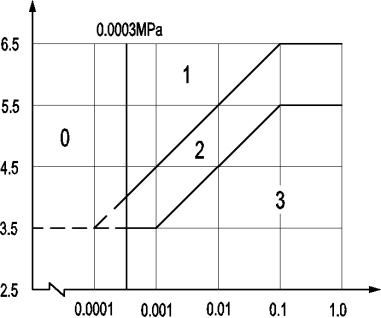
為SSC 1區、SSC 2區和SSC 3區。
圖 3.0.2 碳鋼和低合金鋼 SSC 的環境嚴重程度的區域
0 —0 區;1 —SSC 1 區;2 —SSC 2 區;3 —SSC 3 區
1 酸性環境的嚴重程度為: SSC 3 區> SSC 2 區>SSC 1 區> 0 區。
2 確定含有硫化氫環境的嚴重程度時,應包括在非正常的工況條件下或停工時暴露于未緩沖的低pH 值凝析水相,或井下增產酸液和(或)反排增產酸液等情況。
3 硫化氫分壓和原位 pH 的確定應符合現行國家標準《石油天然氣工業 油氣開采中用于含硫化氫環境的材料 第 2 部分:抗開裂碳鋼、低合金鋼和鑄鐵》GB/T 20972.2 的有關規定。
3.0.1 在制造過程中應對母材和焊縫硬度進行控制和檢測。管材、板材、棒材、鑄件、鍛件等母材的硬度宜選用 HRC 作為驗收指標,測定應符合現行國家標準《金屬材料 洛氏硬度試驗 第 1 部分: 試驗方法(A、B、C、D、E、F、G、H、K、N、T 標尺)》GB/T 230.1 的有關規定,也可采用 HBW、HV 5kg 或 10kg 或其他硬度試驗方法,測定時應符合現行國家標準《金屬材料 布氏硬度試驗 第 1 部分:試驗方法》GB/T 231.1、《金屬材料 維氏硬度試驗 第 1 部分:試驗方法》GB/ T 4340.1 的有關規定。母材硬度換算應符合現行國家標準《金屬材料 硬度值的換算》GB/T 33362 的規定。母材
硬度測定還應同時符合下列規定:
1 硬度檢測點應位于不同位置。
2 鄰近區域讀數的平均值不得大于規定的允許值。
3 單個硬度讀數值不得超過規定允許值的 2HRC。
3.0.2 焊接工藝評定的硬度試驗應按現行國家標準《石油天然氣工業 油氣開采中用于含硫化氫環境的材料 第1部分:選擇抗裂紋材料的一般原則》GB/T 20972.1、《石油天然氣工業 油氣開采中用于含硫化氫環境的材料 第2部分:抗開裂碳鋼、低合金鋼和鑄鐵》GB/T 20972.2、《石油天然氣工業 油氣開采中用于含硫化氫環境的材料 第3部分:抗開裂耐蝕合金和其他合金》GB/T 20972.3和《金屬材料 維氏硬度試驗 第1部分:試驗方法》GB/ T 4340.1中規定的維氏HV10或HV5執行。
3.0.3 現場管道母材和焊縫的硬度檢測應符合國家現行標準《控制鋼制管道和設備焊縫硬度防止硫化物應力開裂技術規范》GB/T 27866 或《高含硫化氫氣田金屬材料現場硬度檢驗技術規范》SY/T 7024 的規定。
3.0.4 酸性環境中不應使用易切削鋼。
3.0.5 本規范中未列出的酸性環境用的碳鋼、低合金鋼、耐蝕合金及其他合金材料應按現行國家標準《石油天然氣工業 油氣開采中用于含硫化氫環境的材料 第 1 部分:選擇抗裂紋材料的一般原則》GB/T 20972.1、《石油天然氣工業 油氣開采中用于含硫化氫環境的材料 第 2 部分:抗開裂碳鋼、低合金鋼和鑄鐵》GB/T 20972.2 和《石油天然氣工業 油氣開采中用于含硫化氫環境的材料 第 3 部分: 抗開裂耐蝕合金和其他合金》GB/T 20972.3 進行評定。
3.0.6 可按現行國家標準《金屬和合金的腐蝕 應力腐蝕試驗 第 7 部分:慢應變速率試驗》GB/T
15970.7 的 SSRT 進行耐蝕合金的篩選評定。
3.0.7 碳鋼和低合金鋼還應評估 HIC 的性能;耐蝕合金在評價抗開裂性能基礎上還應評價點蝕、晶間腐蝕對材料的影響。
4 碳鋼和低合金鋼
4.1 用于 0 區和 SSC 1 區的材料
4.1.1 在 0 區使用的鋼材可不采用抗SSC 的碳鋼或低合金鋼。
4.1.2 用于酸性環境 SSC 1 區的管線鋼性能應符合下列規定:
1 應限制管線鋼的化學成分,保證良好的可焊性。
2 應采用 SMYS 小于等于 550MPa 的管線鋼,且制造和現場焊縫的硬度不應大于 300 HV10。
4.1.3 SSC 1區的材料應采用附錄A中推薦的鋼材,也可采用SSC 2區、SSC 3區的鋼材。
4.2 用于 SSC 2 區的材料
4.2.1 用于酸性環境 SSC 2 區的管線鋼性能應符合下列規定:
1 應限制管線鋼的化學成分,保證良好的可焊性。
2 應采用SMYS小于等于450MPa的管線鋼,且制造和現場焊縫的硬度不應大于280 HV10。
4.2.2 SSC 2 區的材料應采用附錄 A 中推薦的鋼材,也可采用 SSC 3 區的鋼材。
4.3 用于 SSC 3 區的材料
4.3.1 宜采用附錄A中SSC 3區的鋼材。
4.3.2 母材的成分、熱處理和硬度應同時符合下列規定:
1 含鎳量應低于 1%。
2 硬度應小于等于 22 HRC。
3 碳鋼和低合金鋼的熱處理狀態應符合下列中的一種:
1) 熱軋(僅對低碳鋼)
2) 退火
3) 正火
4) 正火加回火
5) 正火, 奧氏體化, 淬火加回火
6) 奧氏體化, 淬火加回火
4.3.3 碳鋼和低合金鋼經冷軋、冷鍛或其他制造工藝進行任何冷變形后,表面纖維性永久變形量大于5%時應作應力消除熱處理。應力消除熱處理的溫度不應低于595℃,熱處理后的硬度應小于等于
22HRC。
4.3.4 焊接應符合下列規定:
1 用于現行國家標準《氣田集輸設計規范》GB 50349 中規定的一級、二級地區的碳鋼集輸管道,SMYS 小于 290MPa 且列于附錄 A 中的非熱軋態金屬材料,可接受焊縫的焊接狀態;SMYS 大于等于 290MPa 的碳鋼、低合金鋼焊縫應在不低于 620℃的溫度進行焊后熱處理。
2 碳鋼、低合金鋼母材和填充金屬的化學成分和焊接參數應按現行國家標準《控制鋼制管道和設備焊縫硬度防止硫化物應力開裂技術規范》GB/T 27866 的有關規定執行。焊縫、熱影響區和母材金屬的硬度應小于等于 250HV10。
3 焊縫和焊接接頭硬度的測定應按 3.0.4 的規定執行。
4 當采用可能導致熔敷金屬中鎳含量大于 1%的工藝和焊材時,應根據現行國家標準《石油天然氣工業 油氣開采中用于含硫化氫環境的材料 第 2 部分:抗開裂碳鋼、低合金鋼和鑄鐵》GB/T
20972.2 進行 SSC 評定試驗合格之后方可采用。
4.3.5 表面處理、覆層、襯里等應符合下列規定:
1 滲氮、金屬涂層(電鍍和化學鍍)、轉化型涂層、塑料覆層和襯里不應用于防止 SSC。
2 碳鋼和低合金鋼的覆層采用焊接、銀釬焊或噴涂金屬等熱加工且基體金屬的熱處理狀態不發生改變時可用于酸性環境。基體金屬升溫超過下臨界溫度,應通過熱處理使基體金屬硬度小于等于
22HRC,基體金屬的最終熱處理狀態應符合 4.3.2 的規定。
3 采用滲氮表面處理,溫度應低于基體金屬的下臨界溫度,最大深度宜為 0.15mm。
4 采用鍍層、覆蓋層、涂層的基體金屬仍應符合本規范抗開裂性能的規定。
4.3.6 螺紋應符合下列規定:
1 螺紋可使用機械切削進行加工。
2 冷成型(滾壓)的螺紋應滿足本章有關原材料的熱處理及硬度要求。
4.3.7 字模壓印標志應符合下列規定:
1 可采用字模壓印如點、波紋線、圓滑的U 形等低應力標志。
2 部件的低應力區(如法蘭外緣上)可采用字模壓印尖銳的標志,如 V 形。高應力區不宜用字模壓印尖銳的標志,使用尖銳標志的字模壓印后應在不低于 595℃的溫度進行應力消除。
5 耐蝕合金及其他合金
5.0.1 用于酸性環境的耐蝕合金及其他合金的產品、部件及焊接等制造工藝應符合本規范的有關規定。奧氏體不銹鋼、高合金奧氏體不銹鋼、馬氏體不銹鋼、固溶鎳基合金、沉淀硬化鎳基合金、鈷基合金、鈦合金、銅基和鋁基合金等材料和使用環境限制應符合現行國家標準《石油天然氣工業 油氣開采中用于含硫化氫環境的材料 第 3 部分:抗開裂耐蝕合金和其他合金》GB/T 20972.3 的有關規定。
5.0.2 奧氏體不銹鋼 3Cr17Ni7Mo2SiN(318)棒材經固溶熱處理后,硬度應小于等于 24HRC。
5.0.3 馬氏體不銹鋼 12Cr13 鑄件或鍛件應采用下列熱處理工藝,硬度應小于等于 22HRC:
1 奧氏體化加淬火或空冷。
2 在不低于 620℃的溫度下回火,隨后冷卻到環境溫度。
3 在不低于 620℃的溫度下回火,但要比第一次回火溫度低,隨后冷卻到環境溫度。
5.0.4 馬氏體不銹鋼焊件應在不低于 620℃的溫度進行焊后熱處理。
5.0.5 沉淀硬化鎳基合金 0Cr15Ni40MoCuTiAlB(3YC7)帶材經固溶處理加冷加工加時效處理后硬度應小于等于 45HRC;3YC7 棒材經固溶處理加時效處理后硬度應小于等于 40HRC。3YC7 的化學成分、力學性能及熱處理制度應符合附錄 B 和現行行業標準《儀表用耐腐蝕彈性合金 第 1 部分:耐硫化物腐蝕 0Cr15Ni40MoCuTiAlB 彈性合金帶材》JB/T 5329.1 的規定。
5.0.6 鈦合金 TC4 鍛態棒材應符合現行國家標準《鈦及鈦合金棒材》GB/T 2965 的規定,經 750℃~
800℃退火或經固溶處理(850℃~900℃,水淬)加時效處理(450℃~550℃,空冷),硬度應小于等于 35HRC。
5.0.7 焊接熱影響區的硬度不應超過母材允許的最大硬度,并且焊縫金屬的硬度應小于等于用作焊接材料的相應合金的最大硬度。
5.0.8 螺紋應符合下列規定:
1 螺紋可使用機械切削進行加工。
2 滿足本規范的耐蝕合金可采用冷成形(滾壓)進行螺紋加工。
5.0.9 字模壓印標志應符合下列規定:
1 可采用字模壓印如點、波紋線、圓滑的U 形等低應力標志。
2 部件的低應力區(如法蘭外緣上)可采用字模壓印尖銳的標志,如 V 形。高應力區不應使用字模壓印尖銳的標志。
6 雙金屬復合管和復合板材料
涉及測試:SSC硫化氫應力腐蝕試驗